From Raw Materials to Finished Products: ChopAid's Quality Control System
- Share
- Issue Time
- Jan 9,2025
Summary
ChopAid's quality control spans from raw material sourcing to finished products, ensuring top standards. We specialize in antimicrobial, non-slip, and PP plastics for kitchen items like cutting boards.
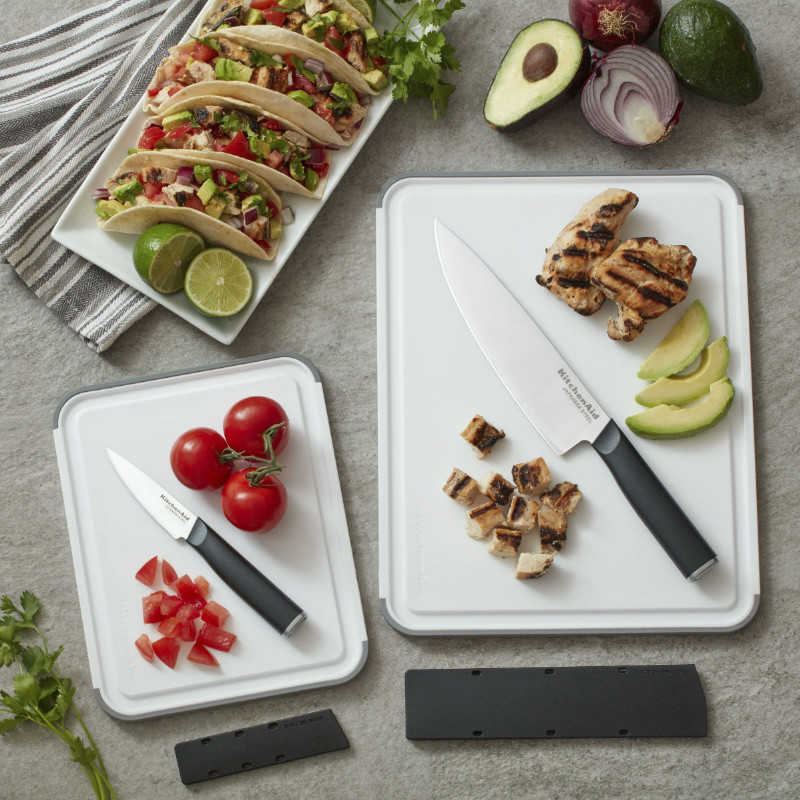
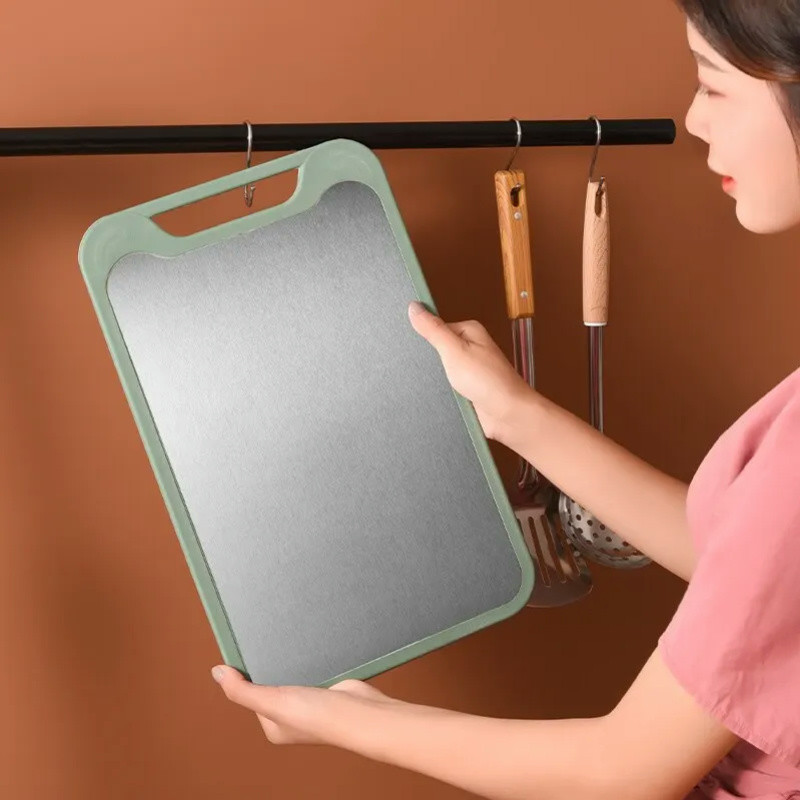
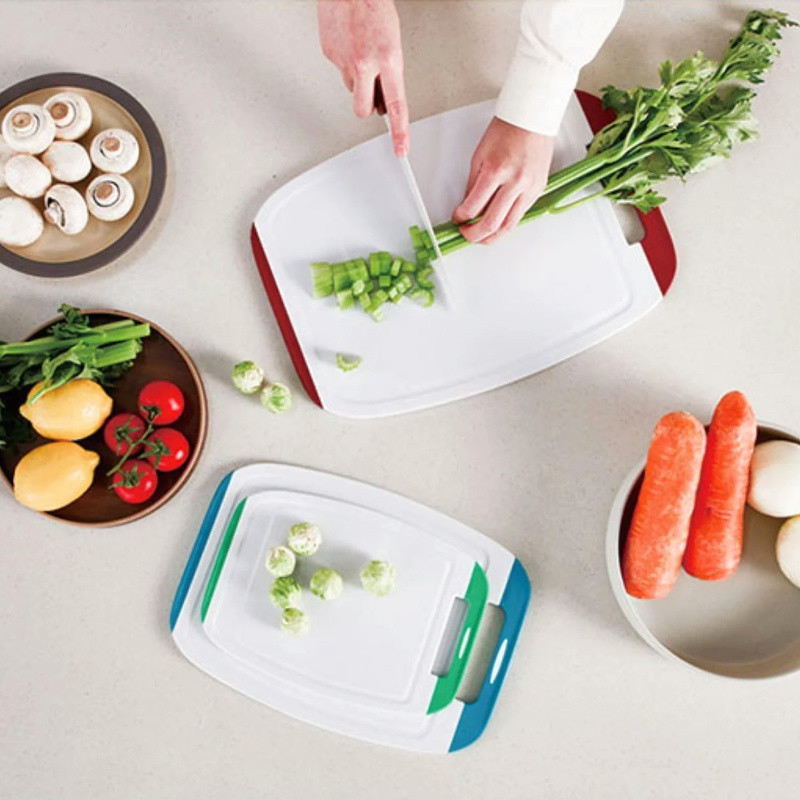
At ChopAid, our quality control system spans the entire production process, from sourcing raw materials to delivering finished products, ensuring that every step meets the highest quality standards. As a company specializing in producing antimicrobial plastics, non-slip plastics, PP plastics, and various other materials for kitchen products such as cutting boards, we understand the critical importance of quality control. This article will provide a detailed overview of the quality control measures ChopAid implements at each stage and explore how these systems ensure superior product standards.
1. Selecting Premium Raw Materials—The First Step in Quality Assurance
The foundation of quality control begins with choosing the right raw materials. At ChopAid, we work closely with the most reliable suppliers in the industry to ensure all materials meet national and international standards. For instance, our antimicrobial plastic materials are certified to ensure they provide effective antibacterial properties during use. Additionally, we perform multiple checks on raw plastics like PP, faux marble plastics, and stainless steel plastics to confirm their durability and environmental sustainability.
We place special emphasis on sourcing baby food-grade plastics, ensuring that all materials meet strict food safety standards, guaranteeing that products used for baby food are non-toxic and safe.
2. Rigorous Quality Monitoring Throughout the Production Process
During production, ChopAid uses state-of-the-art equipment and technology, along with multiple quality inspection stages. Every step of the production line is meticulously monitored to prevent any potential quality issues. Whether producing non-slip cutting boards or eco-friendly plastic materials, we ensure that every process is tested, allowing us to identify and rectify problems immediately.
Furthermore, automated production systems minimize human error, enhancing product consistency and reliability. For example, when producing antimicrobial plastic cutting boards, we use machines to check each product's thickness and antibacterial effectiveness, ensuring long-lasting functionality and effectiveness in real-world use.
3. Product Inspection—Striving for Perfection
Product inspection is a critical component of our quality control system. Before leaving the factory, each cutting board undergoes several tests, including abrasion resistance, non-slip performance, and antibacterial effectiveness. We also perform visual checks to ensure the product's surface is smooth and free from defects. These tests allow us to ensure that every cutting board meets customer expectations and exceeds industry standards.
To further ensure customer satisfaction, we also gather long-term feedback on product performance from the market and consumers. This feedback serves as a valuable tool for refining and enhancing our products.
4. Environmental Responsibility and Safety—Compliance Is Our Duty
ChopAid believes that sustainability is not just an environmental need but a key part of brand reputation. We strictly adhere to international environmental and safety regulations in the production of all our products. During production, we minimize the use of harmful substances and conduct heavy metal content tests on every eco-friendly plastic product to ensure they comply with global environmental standards. Furthermore, all of our products are certified by the FDA, LFGB, and other relevant certifications, ensuring that every kitchen product is safe and harmless.
5. Continuous Improvement—The Driving Force of Quality Control
Quality control is not a static process but a dynamic one that evolves. ChopAid continually improves its existing quality control systems through technological innovations and customer feedback. Our R&D team regularly collaborates with the production team to analyze market needs, refine product designs, and cater to the diverse requirements of our customers. For example, in the design of outdoor cutting boards, we focus on improving convenience and durability, taking into account the real-world usage scenarios of customers in various environments.
Conclusion
From the careful selection of raw materials to precise control during production and extensive testing of finished products, ChopAid's quality control system ensures that every product meets the highest standards of quality and performance. Whether it's non-slip cutting boards, antimicrobial plastic products, or eco-friendly plastics, we fine-tune every step of the process to provide customers with safe, sustainable, and high-quality kitchen products. If you are looking for a trusted cutting board manufacturer, feel free to contact us—we'll provide the best solutions tailored to your needs.
best chopping board for kitchen High Quality Kitchen Artificial Marble Plastic Cutting Board Set
Kitchen Baby Food Double-Sided Plastic Cutting Board | 8 X 12, OEM, ODM, wholesale available for distributors.
Discover our double sided stainless steel and plastic cutting board, with one stainless steel side for cutting meat for durability and one plastic side for cutting fruit and vegetables for odour resistance and hygiene.
Discover our Customisable Meto Plastic Chopping Board (11” x 16”). Featuring a garlic grinder, anti-splash groove, and non-slip design. OEM/ODM available!